生産現場の知恵を集約しヒトに優しい作業空間を構築する
工場の各工程におけるヒトの動作のセンシングに基づき、筋・骨格などの動きを模擬したヒューマンモデルを用いて、作業負荷や難易度を定量化する技術に取り組んでいます。それを活用して、ヒトとロボットとの協働作業分担や作業者の負担が少なくなるように、作業空間の最適化が図れる技術の確立を目指しています。これにより、ヒトにやさしく生産性を高める作業空間のデザインや生産工程の編成を支援します。
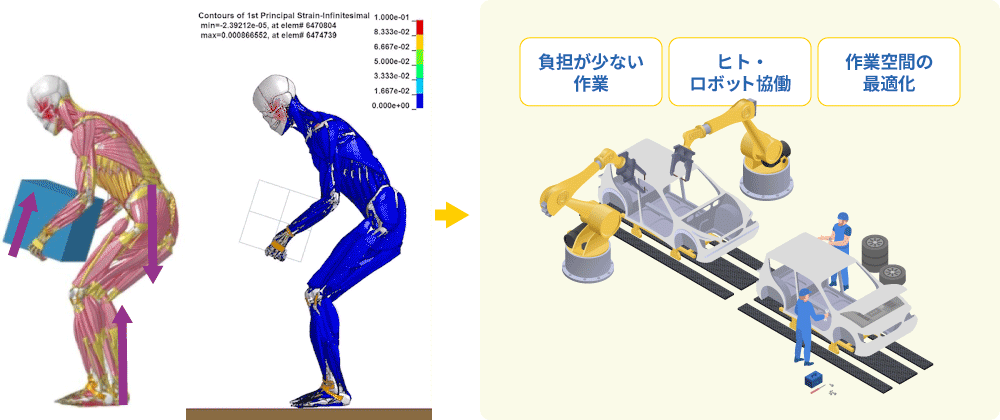
PROJECT 3
気候変動問題の解決のため2050年までにカーボンニュートラルを実現することが世界的に喫緊の課題となっており、トヨタグループにおいても2035年に向けて工場のCO2排出ゼロを目指したチャレンジが進められています。一方、日本国内に目を向けると生産年齢人口の減少と65歳以上の労働参加者の上昇が共に進んでいます。このような背景のもと、モノづくりの現場ではカーボンニュートラルの実現と生産性向上の高度な両立が求められています。
私たちは設備設計や生産計画を、素早く繰り返し評価・解析可能にすることを狙いとして、現実世界の情報をデジタル化して仮想空間上で再現・シミュレーションするデジタルツインの考え方を適用すると共に、熟練作業者のカン・コツや知識を取り入れることができる機械学習モデルの構築を通じ、試作ゼロで柔軟な設計が可能なプロセスの実現を目指しています。さらには作業者や生産設備を含む工場全体のデジタルツイン化を進めることで、エネルギーや生産におけるさまざまな変動要因に対して柔軟に対応できるスマートファクトリを実現し、工場の設計・運用・改善の大幅な効率化を図るための取り組みを進めていきます。
工場の各工程におけるヒトの動作のセンシングに基づき、筋・骨格などの動きを模擬したヒューマンモデルを用いて、作業負荷や難易度を定量化する技術に取り組んでいます。それを活用して、ヒトとロボットとの協働作業分担や作業者の負担が少なくなるように、作業空間の最適化が図れる技術の確立を目指しています。これにより、ヒトにやさしく生産性を高める作業空間のデザインや生産工程の編成を支援します。
一般に車体の試作において、新規部品の設計データから実際の試作品を製作するには長い期間を要します。例えばプレス成形においては、試作品が金型から離れる際に生じる形状の変化は、金型の剛性や加工条件に依存するため、設計データ通りの形状を製作するには多数回の試作が必要でした。私たちは成形後に試作品が金型から離れる際に生じる形状変化を機械学習により予測すると共に、設計データと試作品の誤差を監視しながら成形条件を逐次調整可能なシステムを構築することで、試作ゼロを実現する成形技術の開発を進めています。
電動車の中核部品であるリチウムイオン電池や燃料電池の性能は、内部構造やその均一性など電極膜の品質に大きく左右されますが、高品質な成膜技術の確立は容易ではありません。
私たちがこれまでに培ってきたスラリーや粉体の解析・制御技術とそれらに基づく性能評価技術を応用し、溶媒フリーで成膜可能な革新的な電池製造技術の構築に取り組みます。
世界中でモノづくりにおけるDXやIT化が急速に進展している中、新しい生産方式に対応した自働化・省力化や生産効率の向上、工場全体での省エネルギー化などが求められています。私たちは工場内の生産計画や再生可能エネルギーの需給変動の予測に基づく工場設備や自律搬送ロボットの稼働プランニングなど、仮想空間上での工場全体の最適化の実現を目指し、スマートファクトリの設計と運用が可能なデジタルツインシステムを構築します。
生体医工学,機械力学/メカトロニクス関連,知能ロボティクス,行動環境認識,知能機械システム,設計工学,計測工学,加工学/生産工学,材料加工/組織制御,粉体工学
PROJECT
ハイブリッド材料で二律背反を両立する
稲垣 友美
研究を世の中に届けて
より良い社会の実現へ
土井 慎也
「ガラスの物理」で社会課題に挑む
大山 倫弘
燃焼研究からエネルギーとの関わり方を問う
小坂 英雅
大型研究施設との連携で「小さな孔」を制する
加藤 悟
奇妙な化学現象を非線形数学の視点で解く
長谷 陽子
SiC半導体を極めて量子センサーの実現に挑む
朽木 克博
ポリマーブレンドでエンジニアリングとサイエンスをつなぐ
平井 隆行
二次電池電極から社会の持続可能性を考える
牧村 嘉也
カーボンニュートラルへの取り組み を更新しました
持続可能な社会の実現を目指して
量子の世界とモビリティをつなげる研究
シニアフェロー
飯塚 英男
新しい物理現象を導入して驚きのデバイス・システムを提案する
ナノスケール・センシングシステム
田所 幸浩 ・ 田中 宏哉 ・ 舟山 啓太
人工光合成実用サイズ化を実現させた
異分野融合
人工光合成実用化チーム
新しい概念の結晶成長法で、超低損失な電動自動車を実現する
次世代半導体
シニアフェロー
中村 大輔
実用サイズの人工光合成で
植物の太陽光変換効率を超える
加藤 直彦
未来の技術者へつなぐ「知の襷」
書籍出版
旭 良司/中北 清己
MOVIE CHUKEN 60+
未来に解を
創造性のすべてをより良い社会の実現のために
エグゼグティブアドバイザー
Gill A. Pratt
つながる機器と情報に知能を与え 大規模なシステム群を制御する
自律分散協調制御
戦略研究部門 データアナリティクス研究領域
神保 智彦
人とロボットとAIとが協調・共存可能なより良い社会を実現する
マルチエージェントシステム
戦略研究部門 データアナリティクス領域
西 智樹
人の運動・感覚・感情に関わる脳神経系の構造と機能を数値モデル化する
脳神経系モデリング
戦略研究部門 ヒューマンサイエンス研究領域
岩本 正実
人の自律動作のメカニズムを再現したデジタルヒューマンモデルを構築する
人体自律動作モデリング
戦略研究部門 ヒューマンサイエンス研究領域
中平 祐子
生命の保有する金属イオン認識をヒントに、革新的なレアアース回収プロセスを実証
メタルペプチドプログラム
戦略研究部門 戦略先端研究領域
石田 亘広
モノづくりの常識を打ち破る
スラリー・粉体技術
要素研究部門
スラリー特任研究室